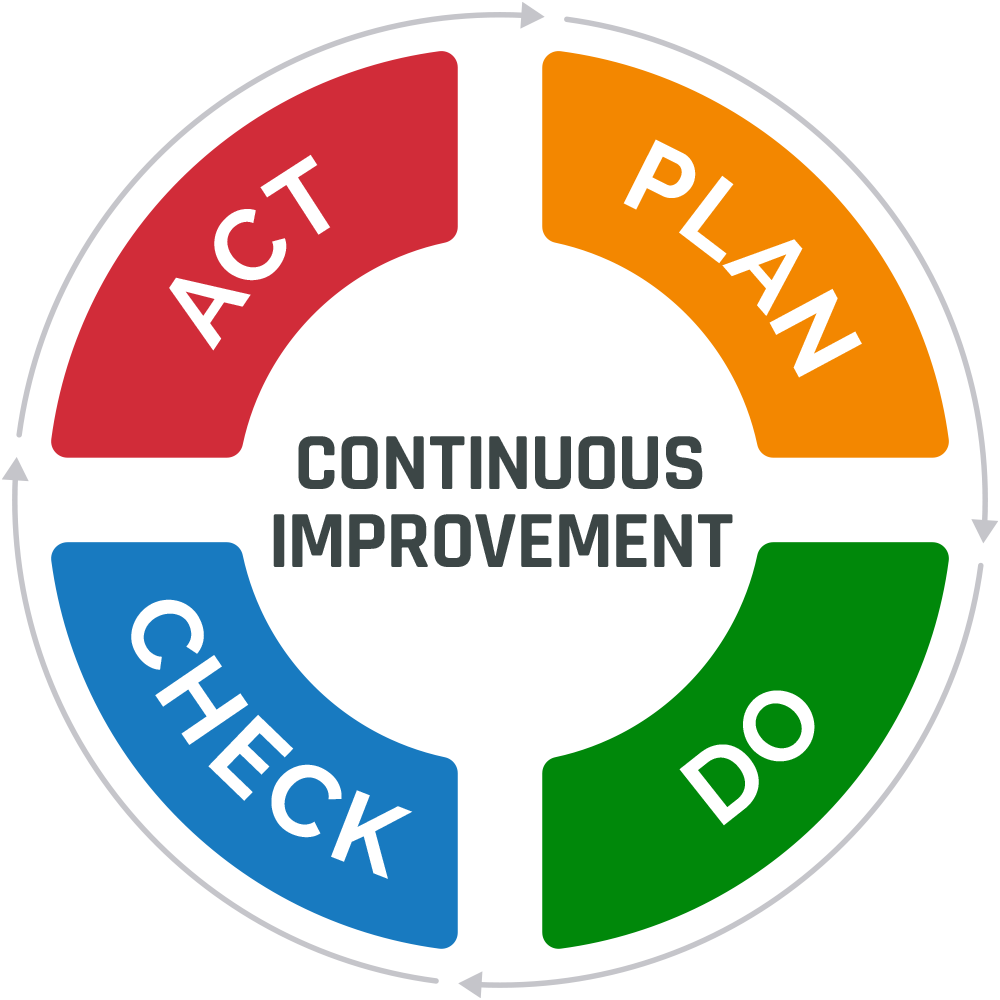
One of the essential elements of a quality management system (QMS) is continuous improvement. It is the process of making ongoing improvements to products, services, or processes through changes that occur incrementally or all at once. Continuous improvement enables organizations to sustain high performance, meet customer expectations, and adapt quickly to changing market conditions.
Regulatory bodies like ISO outline procedures for monitoring, measuring, and analyzing the processes that support a QMS. Similarly, the Medical Device Single Audit Program (MDSAP), which is governed by the FDA and other regulatory bodies across the globe, has published a continual improvement procedure. It provides organizations guidance for evaluating operational performance and identifying areas that need adjustment.
Many of today’s continuous improvement methods stem from Walter Shewhart’s Plan-Do-Check-Act (PDCA) cycle. Using this approach, an organization’s senior management team establishes specific goals and objectives for improvement (Plan). Next, employees implement changes to meet the defined targets (Do). The performance of the changes is measured to determine their effectiveness (Check). If the changes are deemed successful, they are implemented as a standard practice (Act). If the changes are ineffective, the organization will repeat the cycle.
Here, we further explore the various tools and methodologies for measuring performance and driving continuous improvement across your organization.