WHAT ARE THE QUALITY MANAGEMENT ELEMENTS ADDRESSED IN ISO 9000?
The ISO 900O series addresses the essentials of a quality management system (QMS) including processes and procedures that are needed to effectively design, produce, and maintain a product throughout the entire lifecycle. The key elements encompass organizational responsibilities, design and manufacturing processes, equipment maintenance, record keeping, employee training, inspection, and customer relations.
- Management Responsibility
An organization’s management team should develop a quality policy and manual. The quality policy outlines the organization’s strategic goals and mission, whereas the quality manual documents the scope of the QMS.
- Design Controls
Product teams should develop a comprehensive plan for designing and developing the product. User requirements (i.e., inputs) serve as the basis for how the product functions. In turn, documents such as drawings, design specifications, and assembly instructions (i.e., outputs) provide guidance on how the final product is produced. Design changes should be thoroughly documented and reviewed by key stakeholders throughout the new product development process. Additionally, verification and validation testing are necessary to ensure that the finished product meets user requirements and performs as intended.
- Process Control
The development of procedures such as work instructions and assembly instructions is necessary to ensure that products are produced consistently, efficiently, and with fewer errors.
- Document Control
A robust system must be in place to ensure that all product documentation is created, distributed, reviewed, revised, stored, and disposed of in a controlled manner.
- Product Handling
Procedures for the proper storage and transport of products and supplies should by clearly documented and maintained.
- Product Identification and Tracking
Proper labeling is necessary to ensure that products are easily identifiable and traceable throughout the lifecycle.
- Inspection and Testing
All incoming parts and materials must be inspected prior to use. In-process and final inspections should also occur before the finished product is shipped. Records of all inspections should be maintained.
- Corrective and Preventive Actions (CAPAs)
Teams must conduct investigations to identify the root cause of product nonconformities. In turn, countermeasures should be put in place to correct and prevent issues from reoccurring.
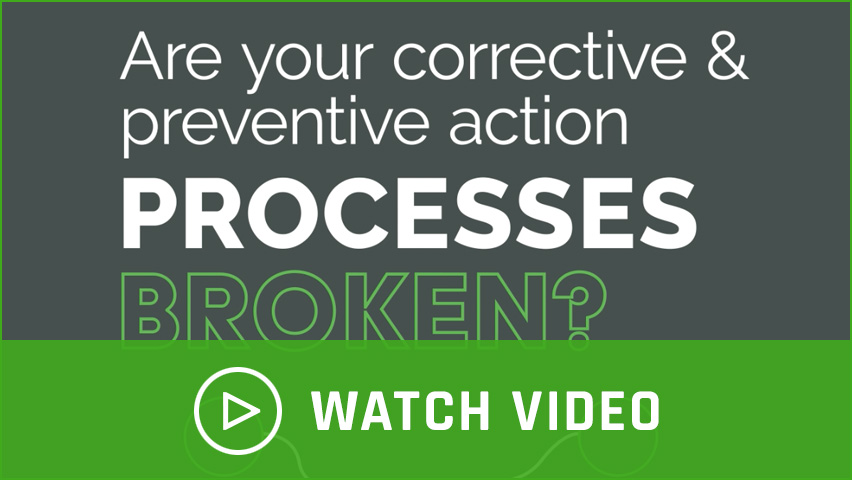